Mastering the Art of Selecting the Best Machining Parts for Your Global Supply Chain
In today's global supply chain landscape, the selection of high-quality machining parts has become increasingly critical for manufacturers aiming to enhance efficiency and competitiveness. According to a recent report by Grand View Research, the global machining parts market is projected to reach USD 200 billion by 2027, reflecting a compound annual growth rate (CAGR) of around 4.5% from 2020 to 2027. As industries continue to adopt advanced technologies and automation, the demand for precision-engineered machining parts is surging, requiring businesses to master the art of selection. This process involves not only evaluating the quality and performance of the components but also considering factors such as supplier reliability, cost-effectiveness, and lead times. By strategically selecting machining parts, companies can significantly streamline operations, reduce production costs, and ultimately gain a competitive edge in the ever-evolving manufacturing environment.
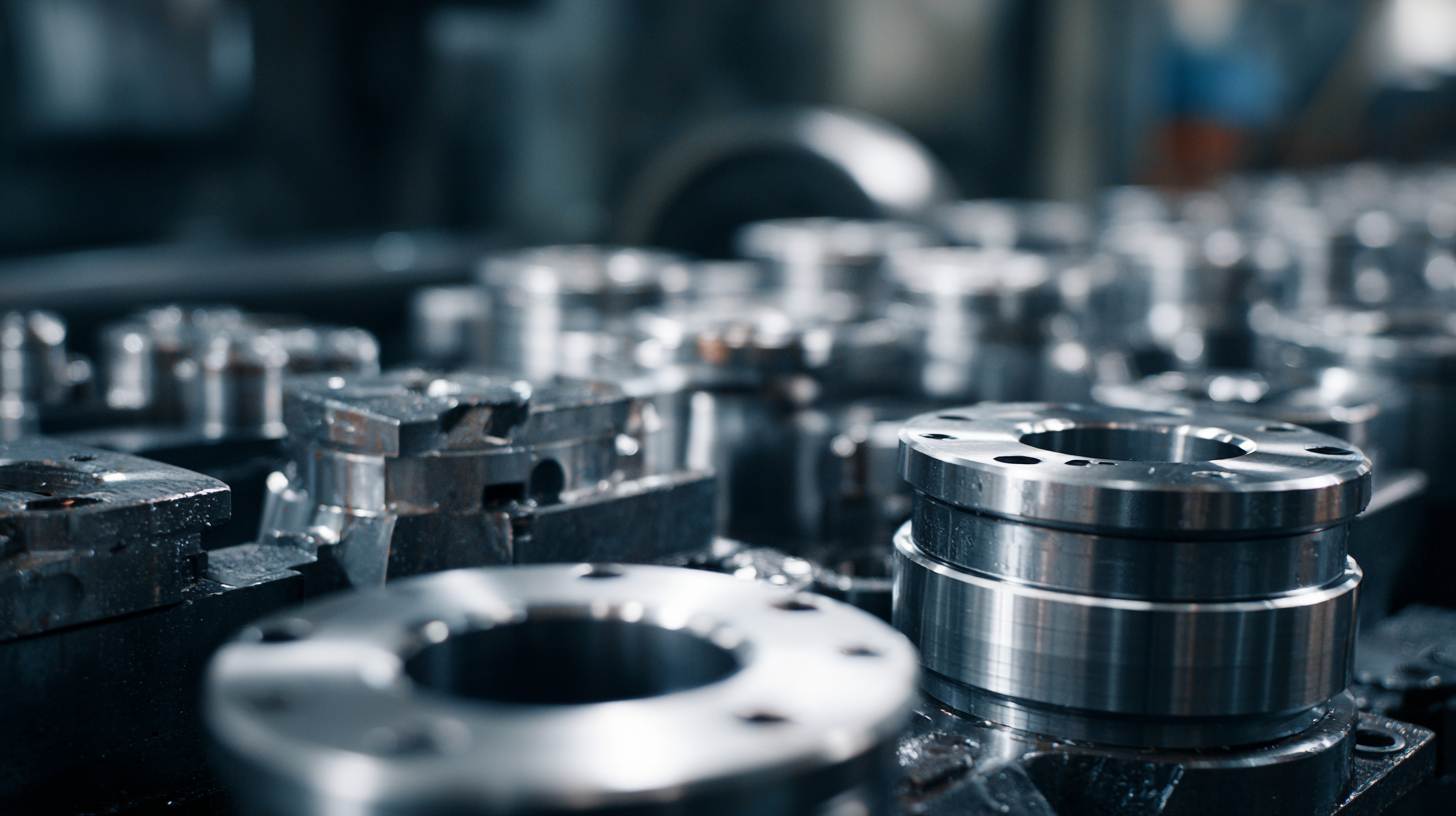
Understanding Industry-Specific Applications for Machining Parts in Global Supply Chains
In today's global supply chain landscape, the selection of machining parts is not just a crucial operational decision but also a strategic one. Industry-specific applications demand a thorough understanding of material properties, tolerances, and finish requirements. A report by MarketsandMarkets estimates that the global machining parts market is projected to grow to USD 166.3 billion by 2025, which underscores the importance of making informed choices that align with specialized sector needs, such as aerospace, automotive, and medical devices.
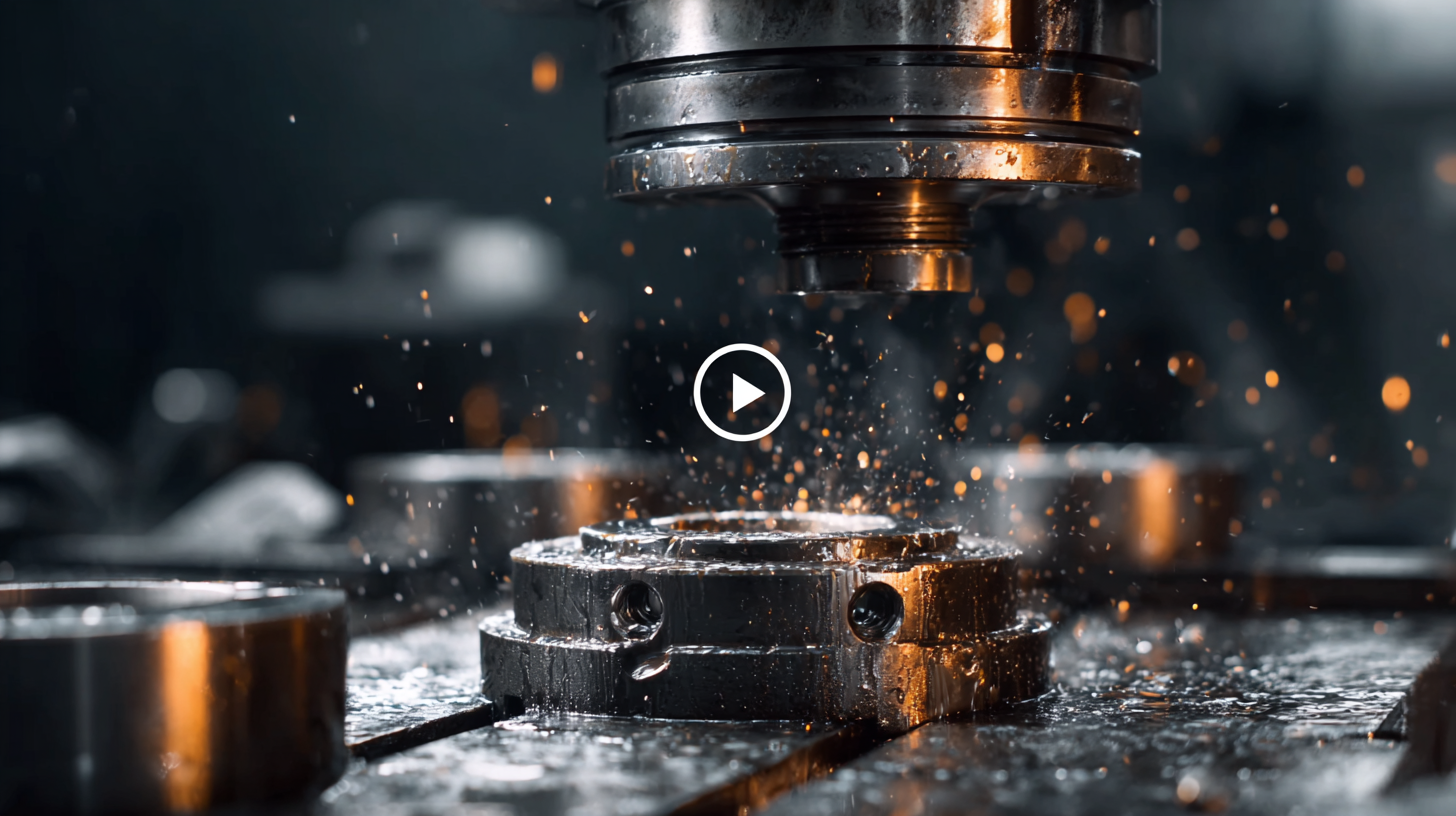
For instance, in the aerospace industry, precision and lightweight materials are paramount. According to a research report from Grand View Research, aerospace components are increasingly utilizing advanced materials like titanium and composites due to their strength-to-weight ratio, essential for fuel efficiency. Additionally, in the automotive sector, the shift towards electric vehicles (EVs) is creating a demand for specialized machining parts that support battery technologies and modular designs. Understanding these sector-specific nuances allows manufacturers to optimize production processes and fulfill the unique requirements of their global clientele effectively.
Key Metrics to Consider When Selecting Machining Parts for Enhanced Efficiency
When it comes to selecting the best machining parts for your global supply chain, focusing on key metrics is essential to enhance efficiency. According to a report by the International Journal of Advanced Manufacturing Technology, companies that prioritize machining part selection can improve operational efficiency by up to 30%. Factors such as material quality, precision, and supplier reliability can significantly influence production outcomes. For instance, using high-grade materials can reduce wear and tear, leading to a longer lifespan for parts and decreased downtime.
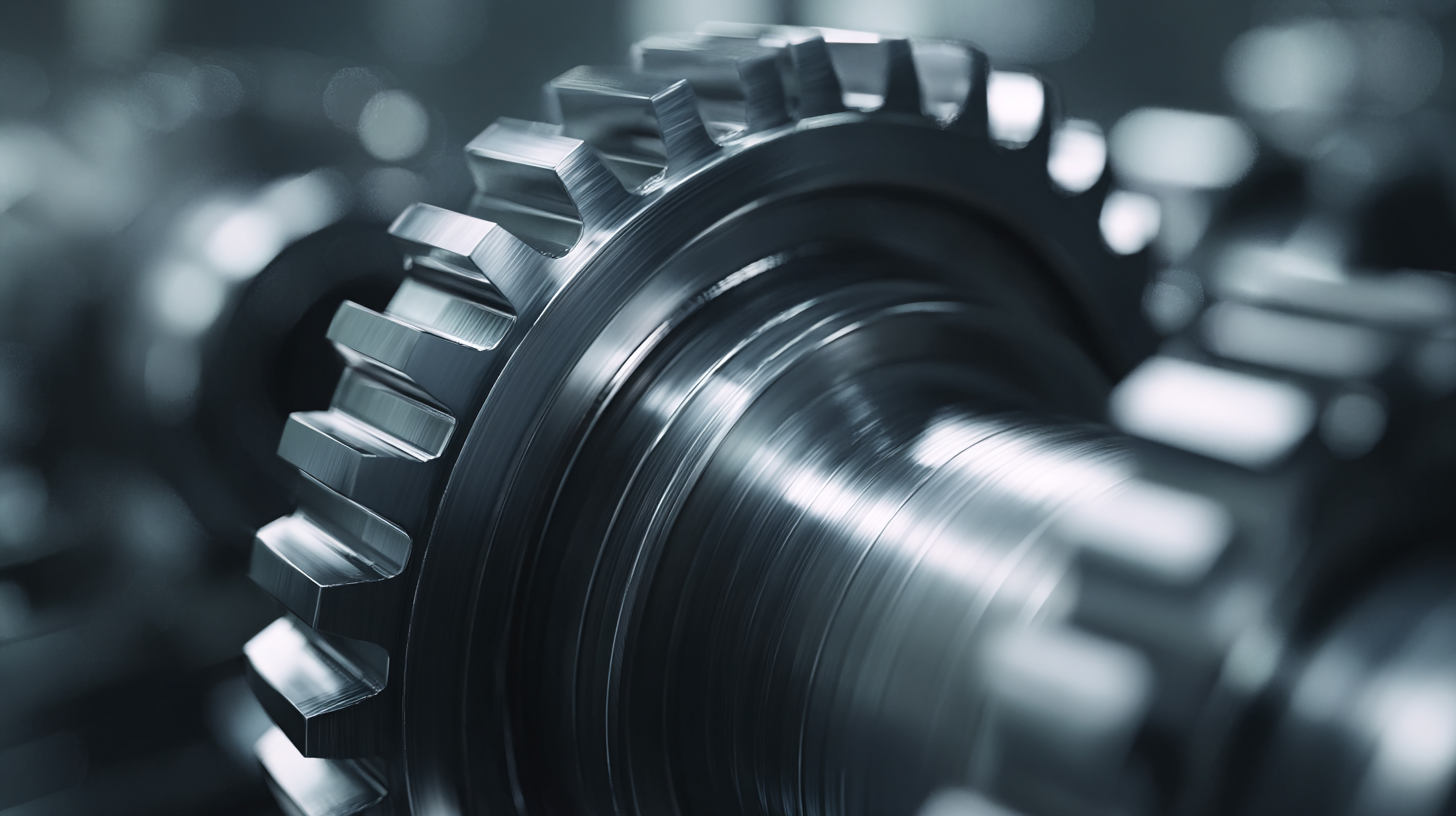
Another critical metric is lead time. A study from Supply Chain Management Review highlights that an average lead time reduction of just 20% can enhance a company’s responsiveness to market changes, resulting in increased customer satisfaction. Furthermore, understanding the total cost of ownership (TCO) is vital. The Aberdeen Group reports that focusing solely on initial part costs can lead to overspending in the long run due to maintenance and replacement expenses. By considering these key metrics—material quality, lead time, and TCO—companies can not only streamline their supply chains but also cultivate a competitive edge in the machining industry.
Exploring Case Studies: Successful Implementation of Machining Parts in Various Sectors
The effective integration of machining parts into various sectors can significantly enhance operational efficiency and product quality. For instance, in the automotive industry, companies have successfully utilized precision machining techniques to develop lighter yet stronger components. A case study involving a leading automotive manufacturer revealed that by adopting advanced machining technologies, they improved fuel efficiency while reducing emissions, aligning with global sustainability goals. This success was largely attributed to their rigorous supplier selection process, emphasizing reliability and technological capability, ensuring that each component met stringent quality standards.
In the aerospace sector, another compelling example showcases how a firm leveraged innovative machining parts to streamline production. By collaborating with specialized manufacturers, the company was able to produce complex components that met the unique demands of aerospace engineering. The resultant parts not only provided superior performance but also enabled faster turnaround times, which proved crucial for maintaining competitive advantage in a rapidly changing market. Such case studies illustrate the importance of strategic partnerships and the role of advanced machining technologies in driving sector-specific success.
Mastering the Art of Selecting the Best Machining Parts for Your Global Supply Chain
Sector | Machining Part Type | Material Used | Success Metric | Implementation Year |
---|---|---|---|---|
Aerospace | Turbine Blades | Titanium Alloy | Increased Efficiency by 15% | 2021 |
Automotive | Crankshafts | Carbon Steel | Reduction in Weight by 10% | 2020 |
Medical | Surgical Instruments | Stainless Steel | Increased Durability by 20% | 2022 |
Construction | Structural Components | Aluminum | Cost Savings of 12% | 2023 |
Energy | Wind Turbine Gearboxes | Alloy Steel | Efficiency Improvement of 18% | 2021 |
Digital Tools and Technologies That Simplify Machining Parts Selection
In today's highly competitive global supply chain landscape, selecting the right machining parts is crucial for operational efficiency and cost-effectiveness. The advent of digital tools and technologies has significantly simplified this process. Advanced machine learning and artificial intelligence techniques can now analyze vast amounts of data to facilitate the supplier selection process, enhance inventory control, and optimize production parameters. For instance, a recent review highlighted that implementing deep learning models can improve decision-making in supply chain management by up to 25%, enabling companies to respond swiftly to market fluctuations.
Furthermore, integrating Natural Language Processing (NLP) can streamline communication across supply chain stakeholders, making it easier to generate insights and forecasts that drive strategic decisions. For example, businesses that adopt AI-driven predictive analytics experience a marked increase in forecasting accuracy, with improvements reported up to 30%. With the right application of these digital technologies, organizations not only elevate their capabilities in selecting machining parts but also position themselves for sustainable growth in an evolving market.
Mastering the Art of Selecting the Best Machining Parts for Your Global Supply Chain
Reasons Why Choosing the Right Machining Parts Determines Supply Chain Success
Choosing the right machining parts is crucial for ensuring the efficiency and cost-effectiveness of your global supply chain. The quality of these components not only affects the performance of the final product but also impacts lead times, inventory costs, and overall supplier reliability. Selecting high-quality machining parts minimizes the risk of defects and service interruptions, fostering a seamless flow in production and delivery.
Tip 1: Always prioritize suppliers with a proven track record in quality assurance. This includes checking their certifications and past performance metrics. A reputable supplier will have stringent quality control processes in place, which translates to more reliable components for your supply chain.
Tip 2: Consider the material composition of the machining parts. Different materials offer distinct advantages in terms of durability, weight, and resistance to corrosion. Aligning material choices with your product requirements can significantly enhance the longevity and performance of your assembled products, leading to greater customer satisfaction.
By focusing on these aspects, businesses can ensure their supply chain operates smoothly, ultimately leading to improved productivity and increased profitability.
Let's Build Together
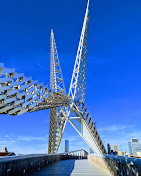
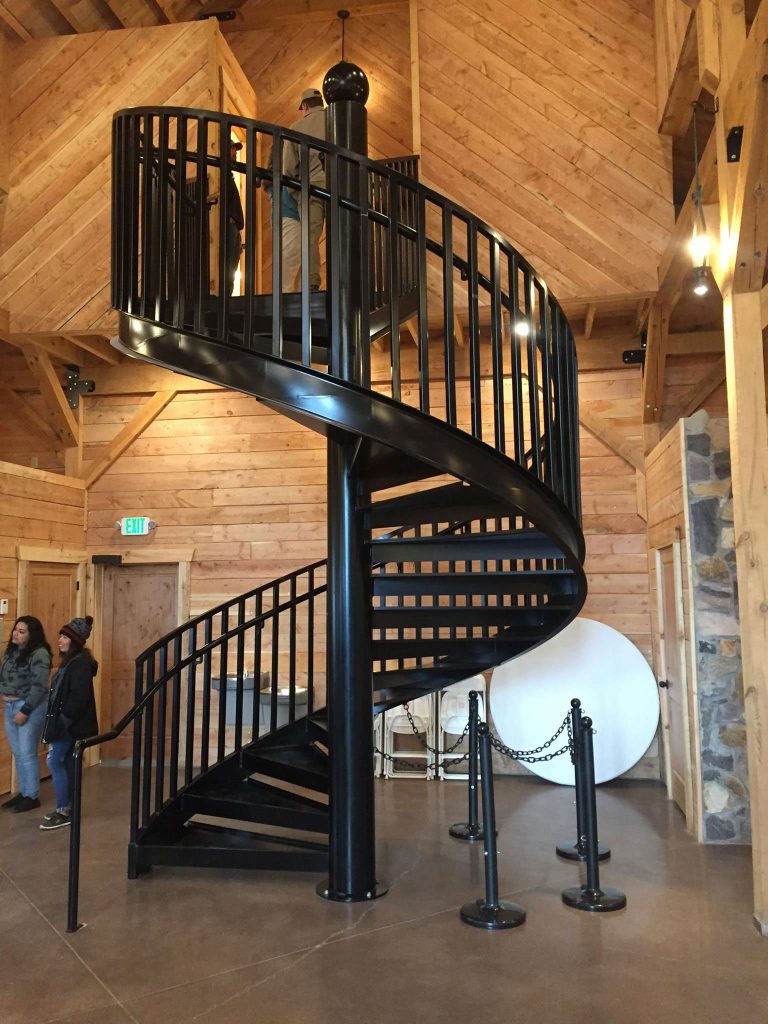
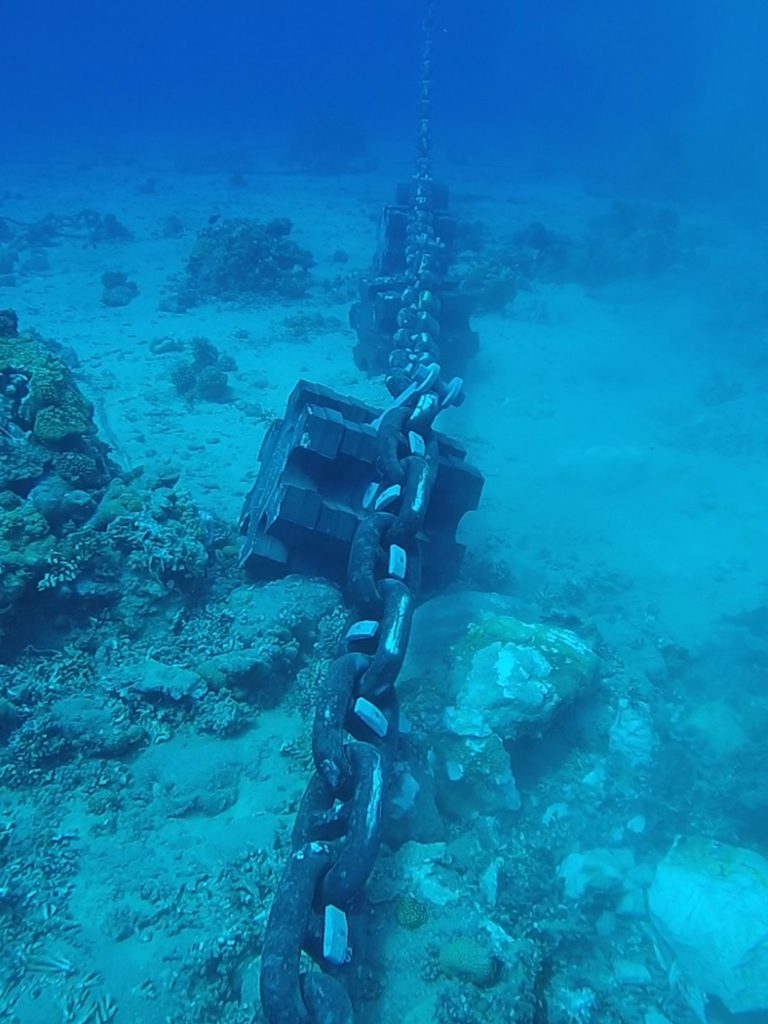
Contact Us: Call 435-563-3503
-OR- Fill in the form below and we will call you back.