Unveiling the Comprehensive Technical Specifications of the Best Large CNC Machine
In the rapidly evolving landscape of manufacturing, large CNC machines have emerged as critical tools for precision engineering and large-scale production. According to a report by MarketsandMarkets, the global CNC machine market is projected to reach USD 100 billion by 2026, with an increasing demand for large CNC machines driven by industries such as aerospace, automotive, and heavy machinery. These sophisticated machines are designed to handle larger workpieces, enabling enhanced efficiency and accuracy. As manufacturers strive to optimize their operations and maintain competitive advantages, understanding the comprehensive technical specifications of the best large CNC machines becomes paramount. In this blog, we will delve into these specifications and highlight the standards set by some of the most reputable manufacturing facilities in China, known for their high-quality output and innovative technology.
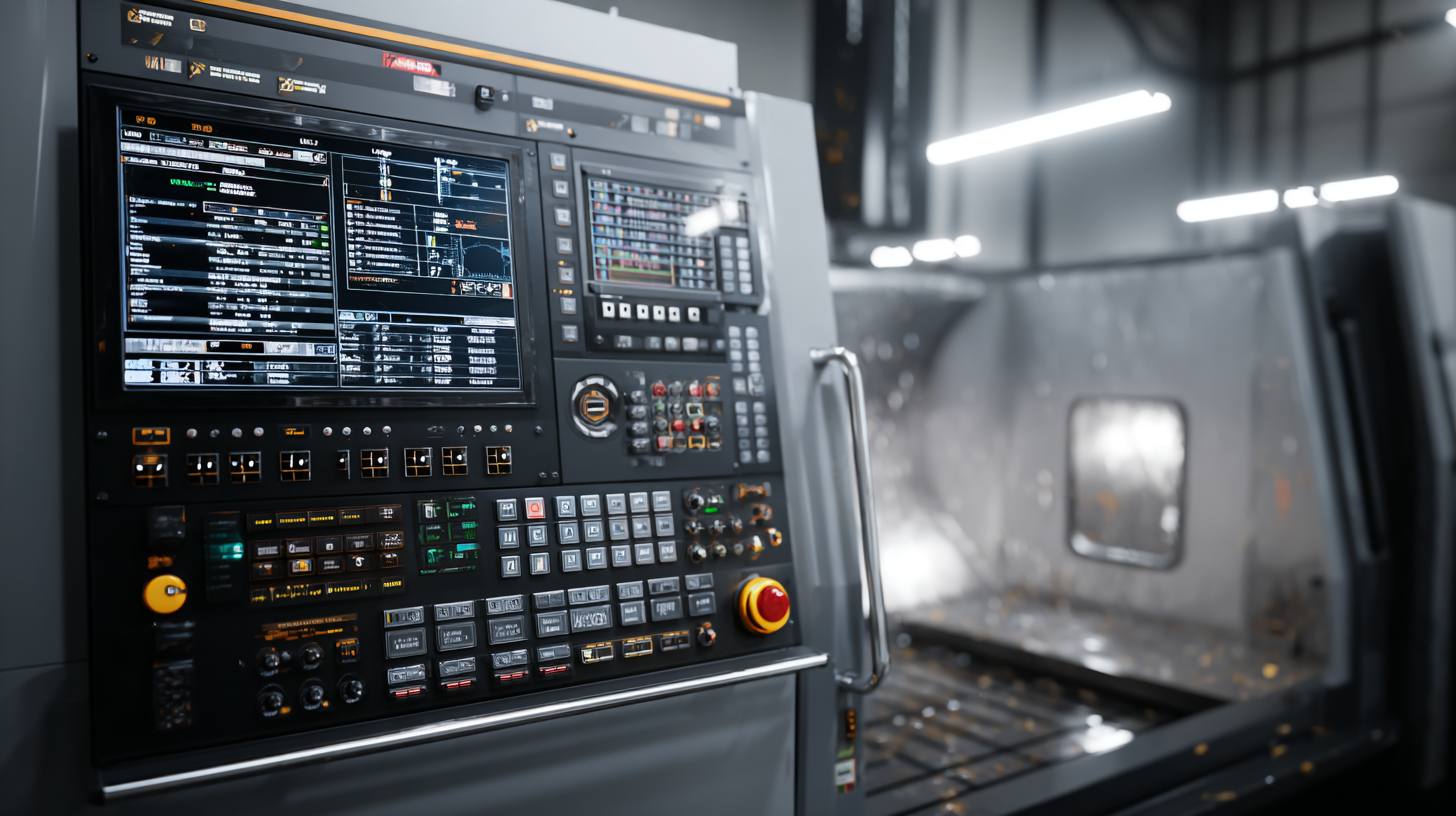
Understanding the Key Features of Large CNC Machines: What to Look For
When selecting a large CNC machine, understanding key features is crucial for making an informed decision. The size and rigidity of the machine's frame are essential for achieving precision and stability during operations. A solid base minimizes vibrations and helps maintain accuracy across various tasks. Additionally, consider the machine's travel range and the types of materials it can effectively handle. This ensures versatility in your projects while maximizing productivity.
Tips: Always check the feed rate and spindle speed specifications. A higher feed rate can lead to faster production, while an optimized spindle speed ensures efficient material removal. Take note of the CNC software compatibility as well; a user-friendly software can significantly enhance workflow efficiency and provide better overall control.
Another vital feature to evaluate is the machine's tooling options. Large CNC machines should allow for various tool attachments to accommodate different tasks without frequent manual adjustments. Furthermore, look for machines equipped with automatic tool changers (ATC) that can enhance multitasking capabilities and reduce downtime. This flexibility not only speeds up production but also allows for more complex machining processes.

Evaluating Precision and Tolerance Levels in CNC Machining
When it comes to CNC machining, precision and tolerance are critical factors that determine the quality of the final product. The best large CNC machines are designed to operate within remarkably tight tolerance levels, often within a few micrometers. This capability is essential for industries where accuracy is paramount, such as aerospace, automotive, and medical manufacturing. Evaluating the precision of a CNC machine involves examining its resolution, repeatability, and the effectiveness of its control systems. High-quality linear guides, robust motors, and advanced software algorithms play a significant role in ensuring that the machine can perform tasks with the utmost accuracy.
Moreover, understanding how tolerance levels are specified is crucial for manufacturers. Tolerance refers to the permissible limit of variation in a physical dimension, and it reflects how closely a part can be machined to its intended specifications. Large CNC machines often feature advanced measurement systems that provide real-time feedback on part dimensions, enabling adjustments during the machining process. This results in reduced scrap rates and enhanced efficiency, as operators can quickly correct any deviations. As technology continues to evolve, the integration of AI and machine learning will further advance the capabilities of CNC machines, pushing the boundaries of precision and tolerance levels to new heights.
Assessing the Material Compatibility of CNC Machines for Diverse Applications
When selecting a large CNC machine, understanding its material compatibility is crucial for optimizing performance across diverse applications. Different industries often require specific machining capabilities, and the right CNC machinery can significantly enhance efficiency and productivity. High-quality CNC machines are designed to work with various materials, including metals, plastics, wood, and composites, each demanding unique cutting tools and techniques.
For instance, machining aluminum requires specific tooling to manage its softness and tendency to chip, while harder materials like titanium necessitate robust tools that can withstand high cutting forces. Additionally, the machine's spindle speed and feed rates should be tailored to the material to prevent issues like overheating or tool wear. Evaluating the technical specifications related to material compatibility will ensure that your CNC machine can meet the demands of your specific projects, from intricate designs to heavy-duty manufacturing tasks. Investing time in understanding these aspects can lead to better decision-making and ultimately unlock the full potential of your machining capabilities.
Unveiling the Comprehensive Technical Specifications of the Best Large CNC Machine - Assessing the Material Compatibility of CNC Machines for Diverse Applications
Specification | Details | Material Compatibility | Applications |
---|---|---|---|
Max Cutting Size | 3000 mm x 1500 mm | Aluminum, Steel, Wood, Plastics | Aerospace, Automotive, Furniture |
Spindle Power | 10 kW | Stainless Steel, Titanium | Medical Devices, Defense |
Max Speed | 24000 RPM | Composite Materials, PVC | Electronics, Display Manufacturing |
Axis Configuration | 3-Axis, 4-Axis Optional | Ferrous & Non-Ferrous Alloys | Custom Fabrication, Prototyping |
Control System | CNC Controller with Touch Screen | High-density Polymers | Artistic Designs, Sculptures |
How to Analyze Cost-Effectiveness and Return on Investment in CNC Manufacturing
When analyzing the cost-effectiveness and return on investment (ROI) in CNC manufacturing, it’s essential to consider not only the initial acquisition costs of large CNC machines but also their long-term operational efficiencies. According to a recent industry report from Grand View Research, the global CNC machine market is expected to reach $100 billion by 2027, indicating a robust demand and potential for profitability. Companies that strategically invest in high-quality CNC machines are likely to see an average ROI of 15-30% within the first few years of operation.
Tips for maximizing ROI in CNC manufacturing include investing in energy-efficient models that consume less power, thus reducing operational costs. Particularly in machining applications, adopting automation technologies can enhance productivity, enabling businesses to optimize their manufacturing processes significantly. Additionally, regular maintenance and timely upgrades can prevent costly downtimes and ensure machines operate at peak performance.
Furthermore, utilizing data analytics to track production metrics can provide insights into cost-saving opportunities. A study from the CNC Trade Association noted that companies employing data-driven decision-making reported a 20% improvement in workflow efficiency. By focusing on these elements, manufacturers can not only improve their production capacity but also secure a healthier bottom line.
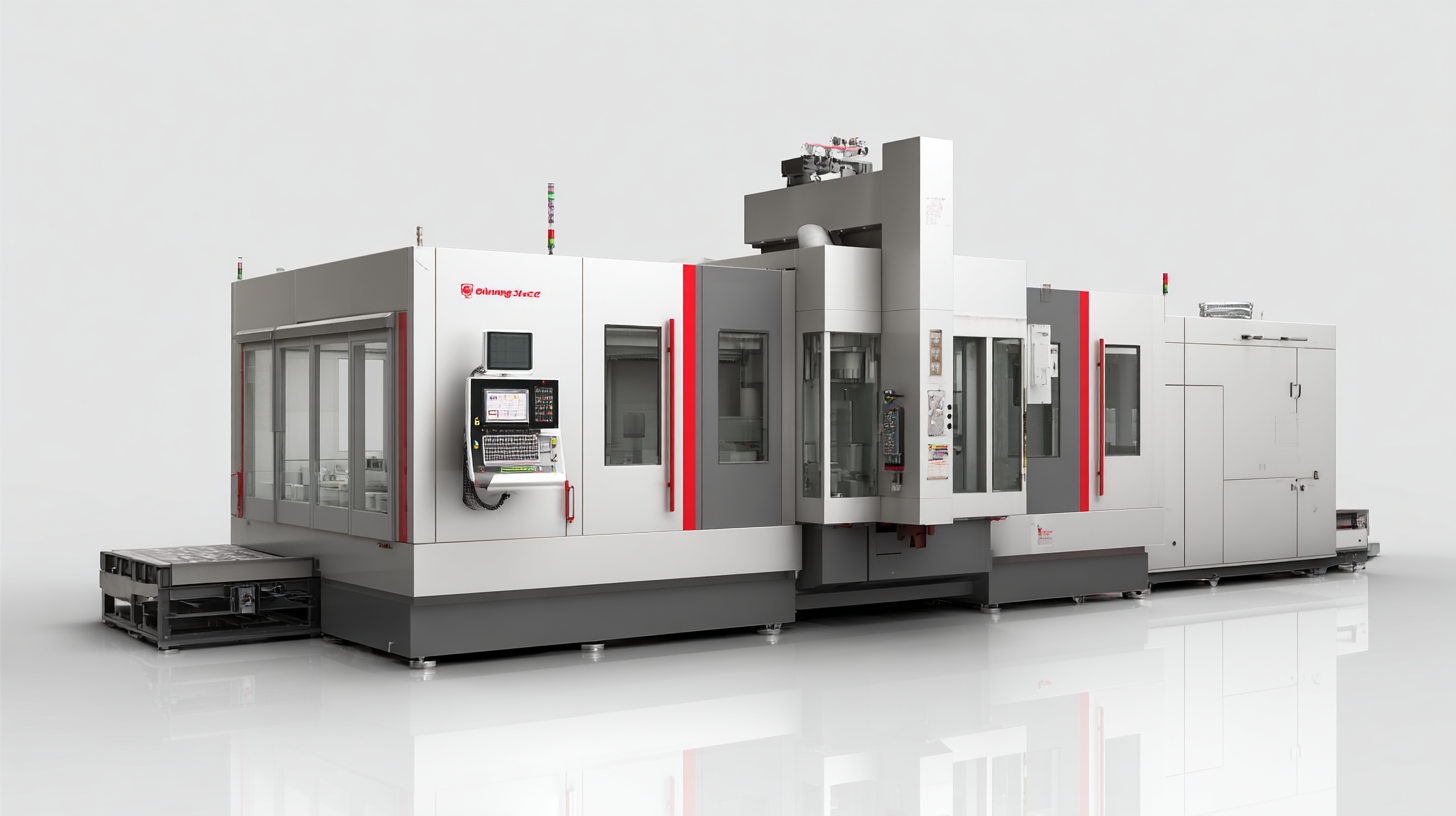
Identifying Trusted Manufacturers: Certifications and Industry Standards to Consider
When choosing a large CNC machine, identifying trusted manufacturers is crucial. Certifications and industry standards serve as key indicators of a manufacturer's reliability and product quality. According to a report by IBISWorld, the machine tool manufacturing industry has seen an annual growth rate of 3.2% over the past five years, with many leading firms acquiring ISO 9001 certification. This internationally recognized standard ensures that manufacturers uphold consistent quality management systems, which is important for maintaining the precision and efficiency of CNC machinery.
Additionally, manufacturers who adhere to standards set by organizations such as the American National Standards Institute (ANSI) and the International Organization for Standardization (ISO) demonstrate their commitment to safety and performance. For example, a study published by Market Research Future emphasized that adherence to these standards not only enhances product durability but also significantly reduces operational downtime, thus promoting higher productivity in manufacturing processes. Evaluating a manufacturer's certifications and compliance with these rigorous standards can provide buyers with confidence in their investment and long-term operational success.
Let's Build Together
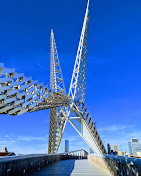
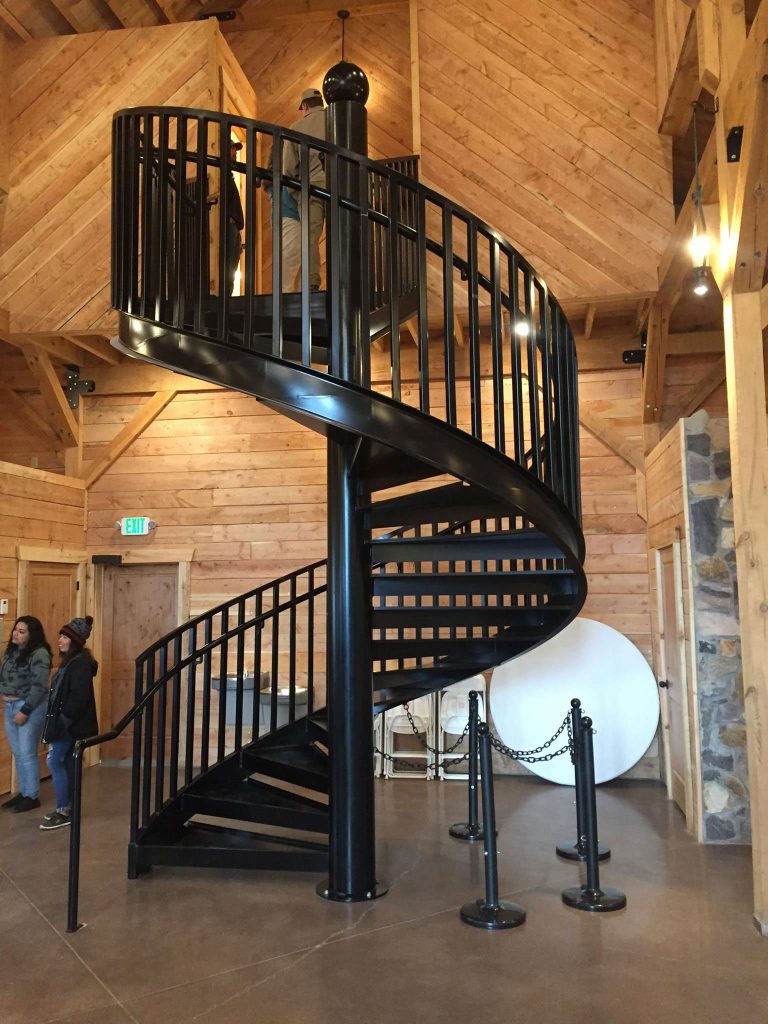
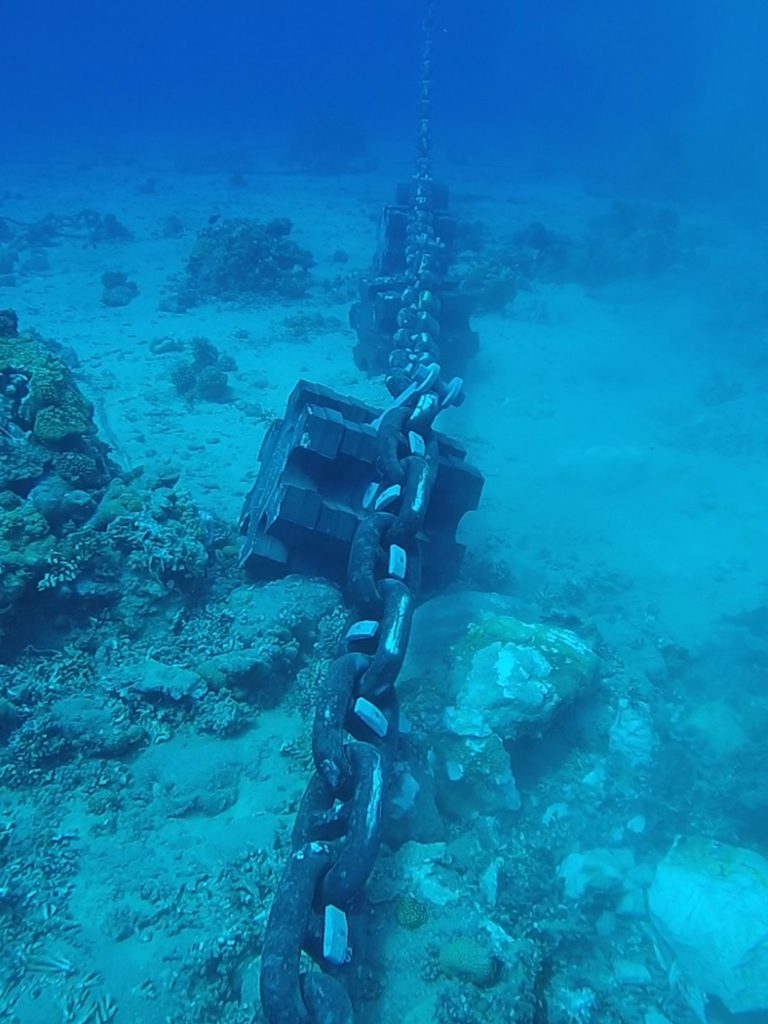
Contact Us: Call 435-563-3503
-OR- Fill in the form below and we will call you back.