Choosing the Right Manufacturer: A Comprehensive Comparison for the Best CNC Metal Products
In today's rapidly evolving manufacturing landscape, the importance of selecting the right manufacturer for CNC metal products cannot be overstated. According to a recent report by MarketsandMarkets, the global CNC machining market is expected to reach USD 100 billion by 2025, driven by the increasing demand for precision components across various industries such as aerospace, automotive, and medical. As companies strive for greater efficiency and cost-effectiveness, understanding the nuances of CNC metal production becomes essential for sustaining competitive advantage.
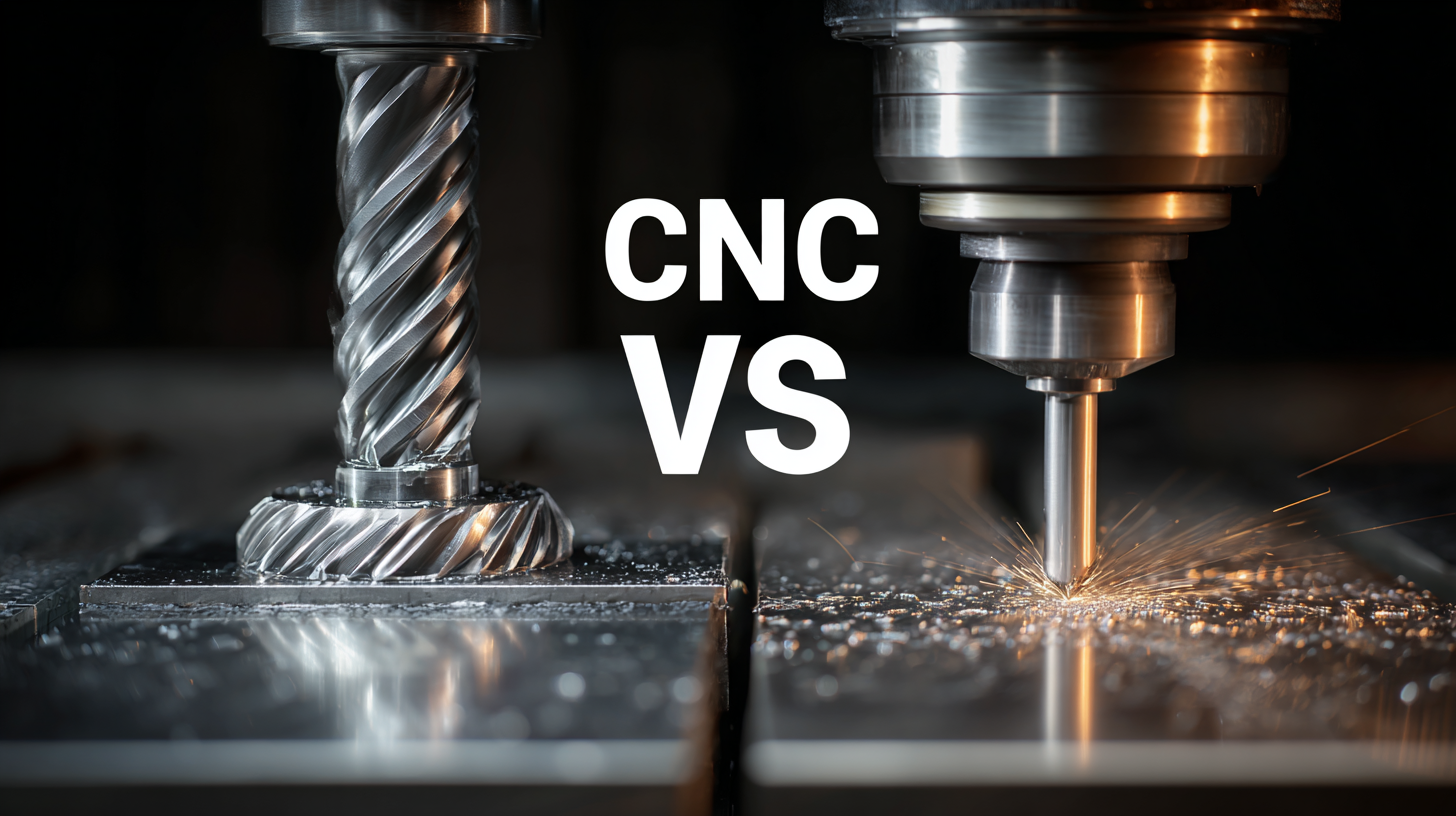
This blog will provide a comprehensive comparison of manufacturers, highlighting key factors such as technology, quality assurance, and production capabilities. By making informed decisions, businesses can leverage the latest advancements in CNC metal fabrication to optimize their operations and enhance product quality.
Identifying Key Factors in Selecting a CNC Metal Products Manufacturer
When selecting a manufacturer for CNC metal products, several key factors must be considered to ensure top-quality outcomes.
First, examining the technological capabilities of potential manufacturers is crucial. Companies that invest in advanced technologies, such as computerized numerical control (CNC) and hybrid manufacturing methods, can offer enhanced precision and efficiency.
As industries continue to embrace automation and Industry 4.0, choosing a manufacturer that keeps pace with technological advancements can significantly impact production quality and lead times.
Another critical aspect is the sustainability of manufacturing practices. With increasing awareness of environmental issues, manufacturers that prioritize sustainable technologies and materials are becoming more desirable.
Assessing a manufacturer's commitment to sustainability can provide insights into their long-term viability and commitment to responsible production. Additionally, manufacturers adept at navigating changes in supply chains and adapting to global market fluctuations ensure greater stability in sourcing, particularly in today's rapidly evolving economy.
By focusing on these key factors, businesses can better identify a manufacturer that aligns with their quality, efficiency, and sustainability goals.
Evaluating Technological Advancements in CNC Machining for 2025
As we look ahead to 2025, the CNC machining industry is poised to undergo significant transformations driven by technological advancements. The global CNC machine market is projected to experience robust growth, increasing from $101.22 billion in 2025 to an impressive $195.59 billion by 2032, with a CAGR of 9.9%. This rapid expansion highlights the importance of integrating cutting-edge technologies, such as artificial intelligence, into CNC operations. The ability to harness AI can enhance precision, reduce operational costs, and improve overall production efficiency, making it essential for manufacturers to adopt innovative solutions to stay competitive.
Tips: When evaluating potential CNC machine manufacturers, focus on those that demonstrate a commitment to technological innovation. Look for companies that are already integrating AI in their manufacturing processes, as they are likely to be at the forefront of advancements in the CNC landscape. Additionally, consider manufacturers that prioritize research and development, ensuring they are equipped to meet the evolving demands of the industry.
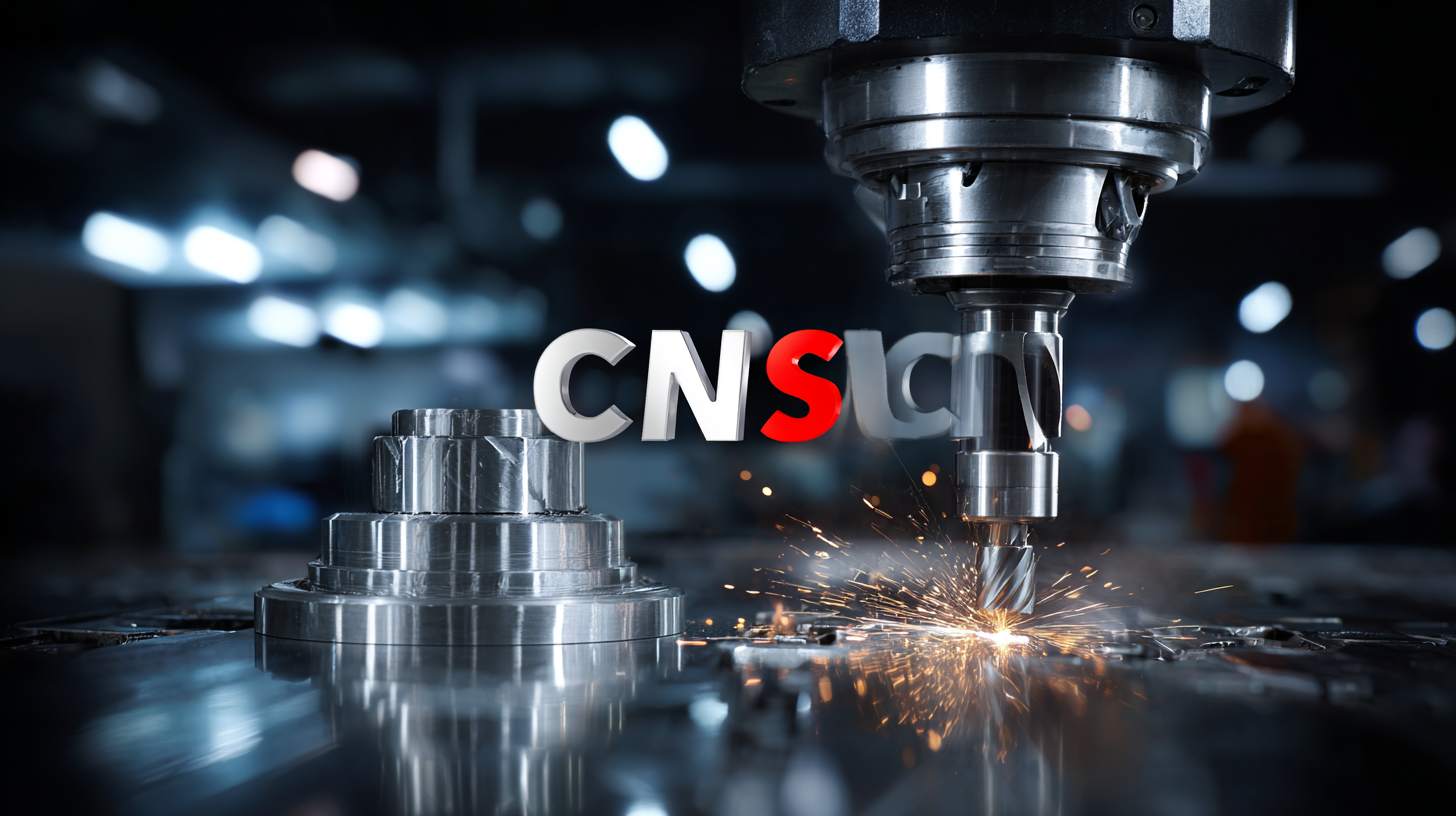
With China emerging as a leading innovator in advanced industries, collaboration with manufacturers from this region could offer unique opportunities to leverage their technological capabilities. By understanding the global landscape, businesses can make informed decisions on which CNC products best suit their needs, ultimately driving growth in a rapidly changing market.
Comparative Analysis of CNC Manufacturers: Quality, Cost, and Capability
When selecting a CNC manufacturer, a comparative analysis is essential to ensure you get the best metal products for your needs. According to a recent report by Grand View Research, the global CNC machining market is projected to reach $100 billion by 2027, highlighting the growing demand for high-quality, cost-effective solutions. Leading manufacturers are distinguished not only by their pricing but also by the capabilities they offer, including precision, material diversity, and lead times.
One key aspect to consider is the balance between quality and cost. A study by Technavio forecasts that the demand for precision CNC machining is increasing, reflecting a preference for manufacturers that maintain high standards while being cost-competitive. Always request samples and test their products to gauge quality firsthand.
Tips: When comparing manufacturers, evaluate their technology and certifications. It may also be beneficial to review customer testimonials and case studies to understand their capabilities better. Additionally, consider their production capacity; a manufacturer with advanced equipment and a scalable process can better meet your evolving needs.
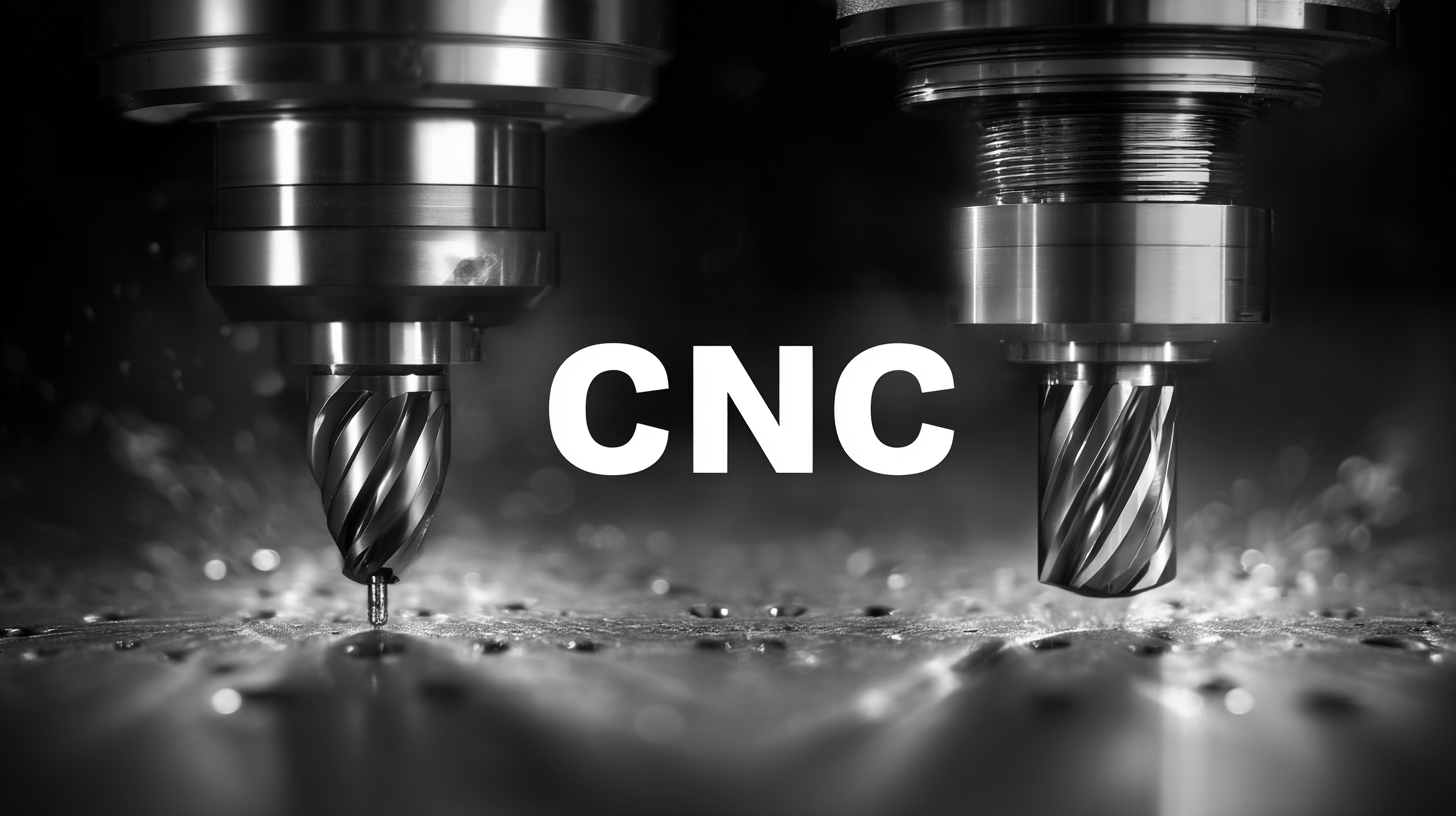
Understanding the Role of Material Selection in CNC Metal Production
In the realm of CNC metal production, material selection is a critical factor that can significantly influence the quality, performance, and cost-effectiveness of the final product. Different materials possess distinct properties, including strength, durability, machinability, and corrosion resistance, which determine their suitability for various applications. For example, aluminum is often favored for its lightweight nature and excellent machinability, making it a popular choice in aerospace and automotive industries. On the other hand, stainless steel is renowned for its strength and resistance to rust, making it ideal for components that need to endure harsh environments.
Choosing the right material involves more than just evaluating physical properties; it also entails understanding the specific requirements of the project. This includes considering factors such as weight tolerance, thermal conductivity, and even aesthetic preferences for visible components. Additionally, collaborating with knowledgeable manufacturers can provide insights into how different materials can enhance the design and functionality of CNC products. By making informed decisions regarding material selection, businesses can optimize their production processes and achieve superior results in their CNC metal products.
Choosing the Right Manufacturer: A Comprehensive Comparison for the Best CNC Metal Products
Manufacturer Type | Material Used | Production Capacity (Units/Month) | Lead Time (Days) | Quality Certification | Price Range ($) |
---|---|---|---|---|---|
Tier 1 Manufacturer | Aluminum Alloy | 5000 | 10 | ISO 9001 | $50 - $100 |
Tier 2 Manufacturer | Stainless Steel | 3000 | 15 | ISO 14001 | $70 - $120 |
Tier 3 Manufacturer | Carbon Steel | 2000 | 20 | None | $40 - $80 |
Specialized Manufacturer | Titanium | 1500 | 25 | AS9100 | $200 - $300 |
Future Trends: Innovations Shaping the Manufacture of CNC Metal Products
The CNC machining industry is on the cusp of significant growth, with projections indicating that the global CNC machine market size is expected to expand from $101.22 billion in 2025 to an astonishing $195.59 billion by 2032. This represents a robust compound annual growth rate (CAGR) of 9.9%. Such growth is driven by advancements in technology and the rising demand for precision-engineered components across various sectors.
As we look toward the future, innovations in manufacturing technologies, particularly in 3D printing, are set to revolutionize the way CNC metal products are produced. Emerging trends indicate that firms that incorporate additive manufacturing techniques are positioning themselves as potential market leaders, with reports highlighting 15 future unicorns in the 3D printing space. By focusing on three key directions—material advancements, automation, and smart technologies—these companies are not only enhancing production efficiency but also pushing the boundaries of creativity and design in metal product manufacturing.
Let's Build Together
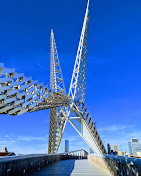
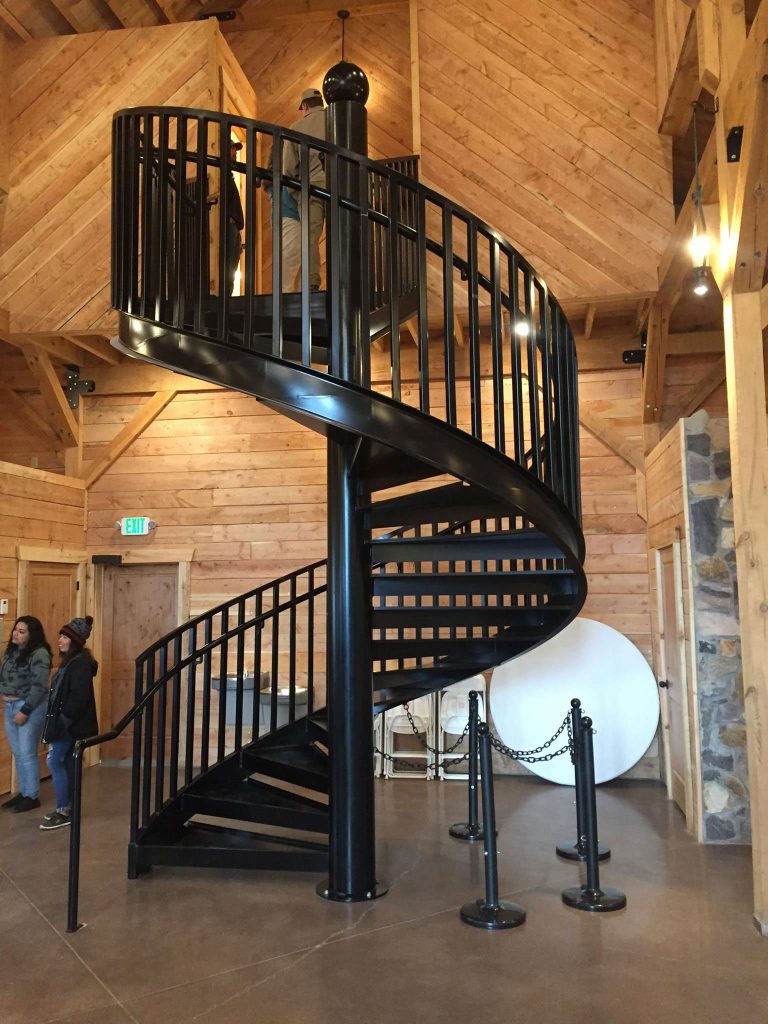
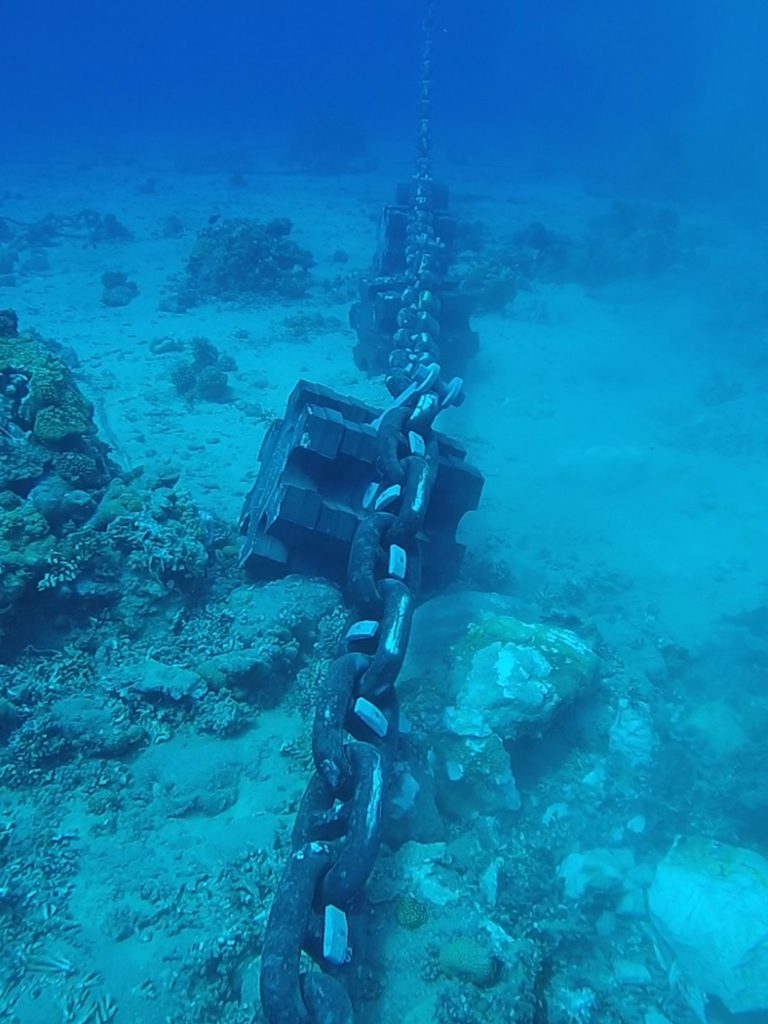
Contact Us: Call 435-563-3503
-OR- Fill in the form below and we will call you back.